Hip-hop, country songs or a classical sonata – for many people, time spent in the car would be almost unbearable without background music. Yet if they listened closely and turned off the radio, they could discover a whole orchestra of different sounds: The airflow sometimes rushes loudly, sometimes softly. The turn signal provides a regular rhythm. The air-conditioning compressor and servo motor hum. The tires squeal during overly violent maneuvers and the parking assistant beeps when the distance becomes too small.
In internal combustion vehicles, however, passengers are unaware of many of these sounds, because the motor drowns out many of the other sound sources. In electric cars, on the other hand, this phenomenon, also known as the masking effect, is largely absent – and presents our team with new challenges.
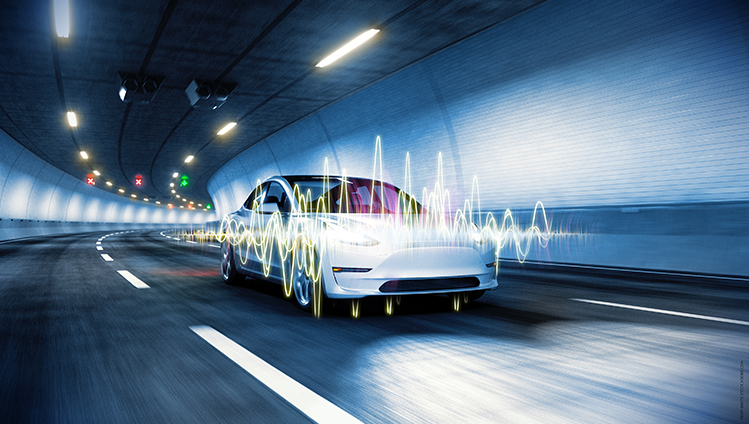
Electric cars don’t drone, they whistle
In the initial developments for eMobility, many vehicle manufacturers had focused on the powertrain and extending the range first. In the meantime, other factors are playing a greater role in the minds of engineers, for example the comfort and well-being of occupants. For, even if the electric drive is objectively quieter than an internal combustion engine, its noises often end up in the four-digit hertz range. And such high frequencies are perceived by people as an unpleasant whistling noise, for example. The reason lies primarily in the different ways the two engines work: an internal combustion engine generates small explosions in each cylinder, while the electric motor drives the e-vehicle with the help of a rotating magnetic field.
When a light vibration turns into a dull tingling
The feeling is also different in eMobility. Anyone who ever sat in an electric car knows that the forces and torques act almost instantaneously, especially when starting off. This is due to the electromagnetic force generation and the higher speed of the electric motor. If the body then starts vibrating and this is amplified by the natural frequencies of the motor housing, this leads to a perceptible phenomenon that manifests itself, for example, as a dull tingling in the stomach area. In this context, engineers also speak of NVH behavior, which stands for noise, vibration and harshness.

To ensure that the body – and its occupants – are shielded as efficiently as possible from these high-frequency excitations from the engine and the road, the electric vehicle engine must be well mounted. And there are plenty of parameters that our mounting professionals can work on, from the design to the material.
With the right design to the optimal timbre
Regardless of whether it is an electric vehicle or a combustion-powered one, an engine mount consists of one connecting element each on the engine and body sides, and an elastic connecting piece that provides insulation. Manufacturers have a free choice here: three- or four-point mounting. Bushing, cone or hydromount. Single or double insulation.
With the aid of simulation methods such as finite element analysis (FEA) and our own material models, our experts can adapt the design and properties of the engine mount precisely to manufacturers' requirements at a very early stage of development, for fine-tuning the “instrument”, subjective and objective NVH analysis methods are also used in the vehicle interior and chassis during the prototype phase.
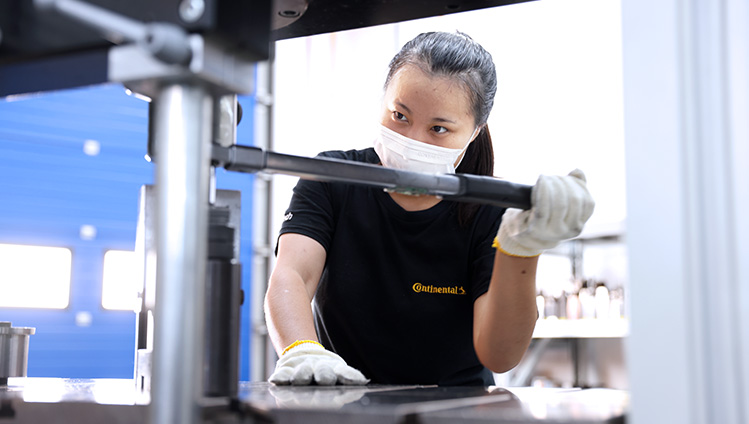
The choice of materials ensures the right pitch in electric cars
But it's not just the design that counts, but also the choice of materials. So, it's all the better that we have real experts on materials in our ranks. Because electric vehicles are already quite heavy due to the large battery packs, the components should be as light as possible while maintaining optimum performance: That way, range is as long as possible. Steel, which can absorb significantly higher forces and torques due to its high specific stiffness, is suitable for the connecting elements. Fiber-reinforced high-performance polyamides, with their low density, are particularly light. And, often, constructions made of aluminum can provide a middle ground between the two extremes.
For the actual insulating element, we can draw on 150 years of experience in rubber. Because here, too, the compounds for electric vehicles differ from those for internal combustion engines: the rubber compound is exposed to lower temperatures in the engine compartment. Therefore, the target conflict of the compound recipe can be shifted towards dynamic hardening and service life. The challenge for the insulation element lies primarily in finding the right stiffness as well as durability for optimum insulation and maximum safety – so that the acoustic experience in an electric car resembles a pleasant sound carpet rather than annoying discords.