Norway is a country of superlatives. In addition to almost 240,000 islands1, 1,000 fjords2, 2,000 waterfalls3 and 200,000 elks4, there are also plenty of electric cars . This isn’t surprising, it’s the result of a strategy: The country has been promoting electric mobility for over thirty years, as green electricity is often cheaper in Scandinavia than gasoline or diesel. The Vikings’ heirs also have the greatest ambitions for the exit deadline: No new passenger cars and light commercial vehicles with combustion engines are to be sold by 2025 at the latest. The conditions are perfect for the transformation to sustainable and low-emission mobility.
Why? Because the weather conditions in a country that experiences 11 meters of snow and temperatures down to -40° C are anything but ideal for electric mobility technology. To ensure that the highly sensitive battery still retains its full performance, hot or cold, our engineers needed to completely rethink temperature management in the vehicle.
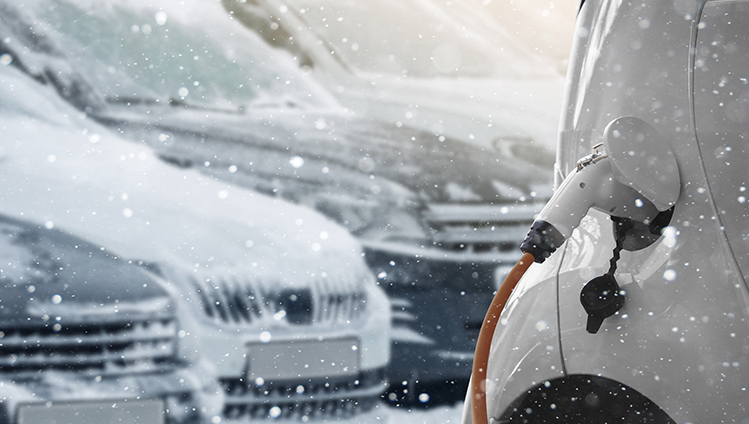
Cold in electric mobility? No thanks!
If you’ve been skiing before, you know that batteries are sensitive to extreme temperatures. This applies to batteries on smartphones as well as to pedelecs and electric vehicles. They simply don’t feel comfortable in the summer heat or winter cold, and extreme conditions generally. Cold in particular slows down the electrochemical processes, the battery voltage drops, and there is a risk of damaging deep discharge for the battery. The problem is that electrical energy that has been lost because the temperature is wrong can’t be recovered. This is why the performance of an electric vehicle battery is highest within a temperature corridor of 15-40°C. And that’s exactly why our line systems directly affect the range of electric cars.
Quite a long (cooling) line
In general, the design of electric vehicles is much less complex than that of those with combustion engines. A gasoline engine with manual transmission has around 1,400 parts, whereas an electric car gets by with just 200 individual components. The exception to this is in the cooling and heating lines. While only the engine itself needs to be cooled in the combustion engine, and the heat generated can be used for cab heating, the line system in the electric vehicle is much more elaborate. Here, the temperature must be managed for several circuits: powertrain, air conditioning unit, and finally the battery.
Depending on the outside temperature, the battery requires either cooling or heating. As a rule, separate systems connected by a heat exchanger are used for this purpose. This doubles the total line length to almost 30 meters compared to the combustion engine. The same applies to the number of necessary socket connections, quick connectors and clamps. In a large commercial vehicle, this can mean almost 100 individual pipes and hoses, plus just as many transition elements.
The main thing is, they’re leak-tight
The most important feature for lines in electric vehicles is absolute leakage integrity. This is because a mixture of water and a coolant flows through the pipes and hoses, such as glycol. The materials used must have the corresponding chemical resistance. In the past, EPDM materials were used for flexible hoses, and aluminum or steel was used for the sturdier tubes. Today, peroxide-crosslinked rubber compounds are increasingly being replaced by thermoplastic elastomers, aluminum and steel by PA, PP or PPS plastics. Depending on the OEM requirement, these materials for the optimal solution can also be combined with each other and connected via appropriate connectors.
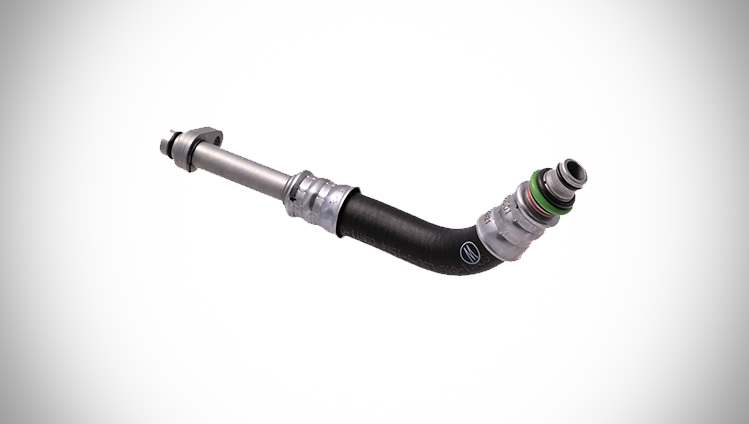
A wide range of expertise is required when working with manufacturers. Established OEMs often have a very detailed and specific idea of the design, which means that more time is invested in the development and approval of material options. Our start-up customers in the eMobility sector like to give our engineers more design freedom and rely on our many years of expertise when selecting materials for hoses, pipes and so on.
Sustainability + electric mobility = the future
As always with electric mobility, the topic of sustainability plays a special role with regard to materials as well. Not only because end consumers are attaching more and more importance to conserving resources and long product lives. Fortunately, the lines in a vehicle are generally designed in such a way that they do not have to be replaced. This by itself reduces resource consumption. In addition, our developers pay particular attention to the weight of the components. Because of the high battery weight, every possible gram needs to be saved elsewhere. With new materials which are just as rugged and leak-tight as their predecessors despite lower wall thickness, we have already been able to save more than fifty percent in weight.
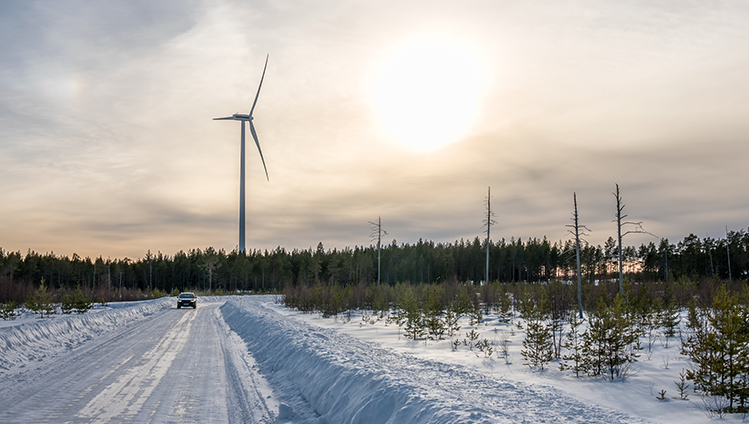
Sustainability is also a trump card in Continental’s own production. We want to neutralize our CO2 load worldwide through negative emissions – including production, the supply chain, and the end of the life cycle. Our focus here is on vehicles without drive emissions. And that’s no little challenge. Because most lines and hoses, whether EPDM, TPE or other plastics, consist not only of a single layer, and the incorporated reinforcing ply is difficult to separate from other layers. Nevertheless, monolayers are entirely conceivable. Recycled granulate, for example from old PET bottles, could also be used. Our material experts see a lot more unused potential here. And here is where the circle closes: Green Norway is taking its recycling obligations very seriously – the first recycling facility for batteries made of electric cars in Fredrikstad is due to start operating soon.
1https://www.laenderdaten.info/inseln-nach-land
2https://www.visitnorway.com/things-to-do/nature-attractions/fjords/the-fjords-explained/
3https://www.worldwaterfalldatabase.com/country/Norway/list
4https://www.nordlandblog.de/elche-norwegen-beobachtung-safari/