Stade de France, Paris, França. 3 de agosto de 2024. 22h30 "Em suas marcas!" É incrível como uma multidão de 80.000 pessoas consegue ficar em silêncio em questão de segundos. Daria para ouvir um alfinete caindo no chão não fosse pelas vozes abafadas dos repórteres de rádio e TV na tribuna de imprensa e os nove corpos atléticos assumindo lentamente suas posições, agachados nos blocos de partida. Os próximos dez segundos determinarão se anos de esforço valerão a pena — se eles aproveitarão a única chance na vida da glória olímpica. "Preparar!"
Para chegar até aqui, esses atletas tiveram de prestar atenção em cada detalhe, praticamente sem espaço para erros. Milhares de horas na pista. Milhões de quilos levantados na academia. Centenas de sessões dolorosas na fisioterapia. Programações rígidas e cuidadosas para todos os aspectos da vida, desde padrões de sono até alimentação. Sem falar nos equipamentos: além dos equipamentos de corrida perfeitamente ajustados, foi necessário testar dezenas de pares de sapatilhas de corrida, tão leves que mal são percebidas, mas que ainda transmitem o máximo de potência quando a prova começa. Tudo na esperança de que o esforço compense, de que a máquina humana não fique sobrecarregada e funcione na melhor forma possível quando realmente é necessário.
Há outra área em que peso e atenção aos detalhes têm um papel igualmente importante: os carros. Ao longo dos anos, eles passaram a ser atletas de ponta, ganhando "músculos automotivos" – mas às custas de mais massa. E, como as agências reguladoras, como a União Europeia, estão forçando os OEMs a reduzirem as emissões de carbono de todas as frotas, eles, por sua vez, estão procurando maneiras de melhorar o condicionamento dos seus atletas de ponta – uma peça leve por vez. Deixe isso com os técnicos da Continental.
Parceria com especialistas em leveza
Nossos especialistas em perda de peso automotivo estão em Rennes, França. Há dez anos, eles começaram a procurar maneiras de desenvolver peças leves que tivessem um desempenho tão bom quanto as soluções tradicionais – e encontraram uma abordagem possível no setor da aviação. Lá, os engenheiros têm usado compostos em componentes grandes há muito tempo. Por que isso também não passa a ser uma solução em aplicações automotivas?
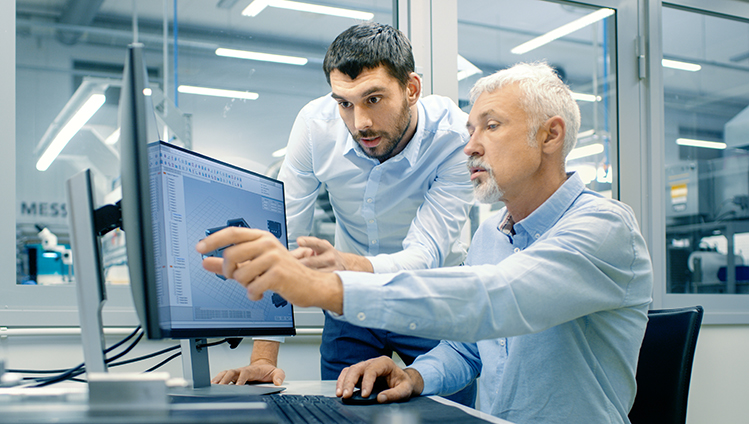
Dessa forma, eles se uniram a outros pioneiros no campo de materiais leves para combinar as experiências em sistemas antivibração, borracha e termoplásticos com o conhecimento do setor aeronáutico em compostos termoplásticos e processos automatizados para disposição de fibras. Adicione o conhecimento de pesquisas mais recentes de duas universidades e – voilà – você tem a Dynafib, uma nova solução de material para peças automotivas.
Peças resistentes com menos massa – a Dynafib garante a perda de peso automotivo
Dynafib é uma tecnologia leve que consiste em várias camadas de fita em um laço fechado. A fita é feita de centenas de fibras de vidro muito longas, todas alinhadas na mesma direção, impregnadas de uma matriz termoplástica e depois fundidas com a ajuda de um feixe de laser. Quanto mais forte e resistente uma peça precisa ser, mais camadas poderão ser usadas. É por isso que a Dynafib é especialmente indicada para peças que precisam suportar cargas internas voltadas para fora, como hastes de torque.
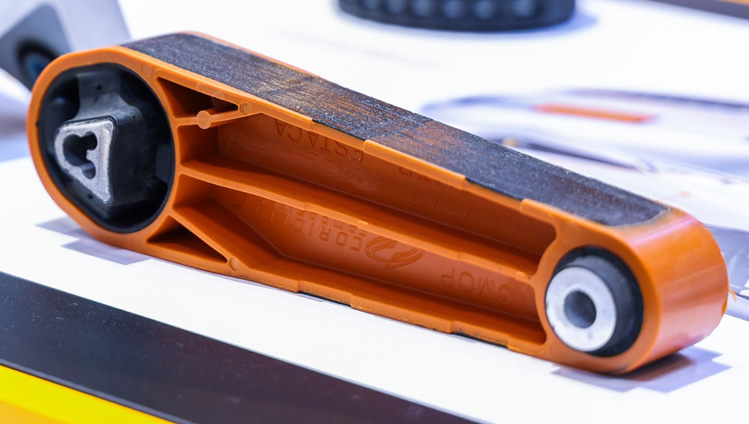
Elas são um exemplo perfeito para ver mais de perto o potencial da Dynafib e diminuir o peso e, ao mesmo tempo, manter o desempenho. As hastes de torque normalmente são feitas de aço ou alumínio e amortecem o impacto do torque em um veículo, evitando a vibração e a transferência de ruído, além de restringir o rolamento do motor. Para unir com segurança todas as peças do componente, a haste reforçada com Dynafib é combinada com as duas buchas e depois moldada com poliamida, o que aumenta a funcionalidade estrutural da peça. Como foi projetado especificamente para essa aplicação, o reforço em Dynafib evita que a haste de torque se rompa e aumenta muito sua resistência com muito menos peso.
Mas quanto a menos? Vamos usar uma haste de torque de alumínio como referência para nossa comparação. Uma haste de aço com a mesma resistência seria aproximadamente 20% mais pesada. Uma haste de torque termoplástica que não tenha sido reforçada atinge cerca de 75% do peso de uma haste de alumínio, mas também com apenas 50% de sua resistência. Somente a solução Dynafib leve atinge os mesmos valores de resistência das versões metálicas, ao mesmo tempo em que reduz em aproximadamente 50% o peso em comparação com o alumínio.
Desafios durante o desenvolvimento de novas tecnologias leves
Embora seja uma tecnologia altamente inovadora, infelizmente, a Dynafib não é indicada para todas as aplicações ou componentes automotivos. Em geral, somente peças que possam ser reforçadas com uma única fita reta podem ser levadas em consideração, pois a fita Dynafib não pode sofrer torções. Além disso, o processo de produção precisava ser pensado porque tínhamos que garantir que todos os componentes fossem unidos corretamente otimizando a injeção de plástico.
O tamanho do componente também é um desafio. Já faz muitos anos que os players do setor da aviação têm produzido superfícies grandes com curvas suaves usando diversas camadas de fita multidirecional. No entanto, a produção de um componente leve tão grande demora muito. E o tempo é fundamental, pois é uma das principais demandas do setor automotivo, além dos custos, no desenvolvimento de peças. Por isso, o número de peças que precisam ser produzidas a baixo custo é muito maior do que os números de produção de um cockpit de avião. Para que valham a pena, as hastes de torque em Dynafib precisam ser colocadas em uma presilha elevada de 20 a 30 segundos por unidade.
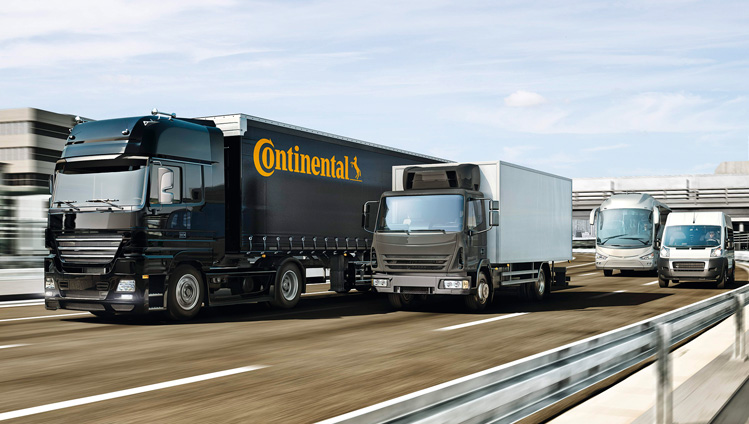
Portanto, haverá muitas coisas a serem levadas em consideração se você quiser trocar uma peça metálica padronizada por novas tecnologias leves. No entanto, enquanto a barra de torque em Dynafib da Continental entrará em produção em massa neste trimestre, nossos especialistas em materiais e produtos em Rennes já estão trabalhando em como reduzir outros componentes automotivos, como braços articulados e molas pneumáticas. Dessa forma, esperamos diminuir aproximadamente um terço do peso inicial aplicando Dynafib.
E embora tenham até agora apostado nos veículos de passageiros, os técnicos da Dynafib já se aventuram pelo mundo convencidos de que também existem outros veículos que se beneficiariam da perda de peso: caminhões, máquinas agrícolas, máquinas de construção, bondes e trens, bicicletas e outros equipamentos de mobilidade leve. Sem contar outras aplicações industriais que não incluam o espectro da mobilidade – o leque de possibilidades para soluções leves é quase tão amplo quanto o número de eventos para o trimestre mágico de 2024 na capital francesa.
O futuro: soluções leves e sustentáveis
A perda de peso obviamente não é um fim em si, nem para atletas na pista nem para carros. Para OEMs, o exercício tem uma finalidade: a sustentabilidade. Um veículo mais leve acarreta menos consumo de combustível e, assim, menos emissões de CO2. Mas, na Continental, não olhamos apenas para a cadeia de valores posteriores, mas também para nossos próprios materiais, soluções e processos. O que é excelente na Dynafib é que o processo de produção propriamente dito não consome muita energia. No entanto, a pegada de carbono ainda não está onde gostaríamos, principalmente por causa dos materiais usados: fibra de vidro e termoplásticos novos.
Nossos especialistas em Dynafib em Rennes também estão trabalhando nisso. Eles esperam introduzir, em dois anos, uma nova solução leve usando a tecnologia Dynafib com materiais de base biológica e polímeros reciclados que reduziriam a pegada de carbono geral a apenas uma fração do que é agora. Um verdadeiro peso leve com força total. E, até lá, talvez alguns deles estejam entre esses 80.000 torcedores comemorando quando o tiro da largada for dado em Paris. "Já!"